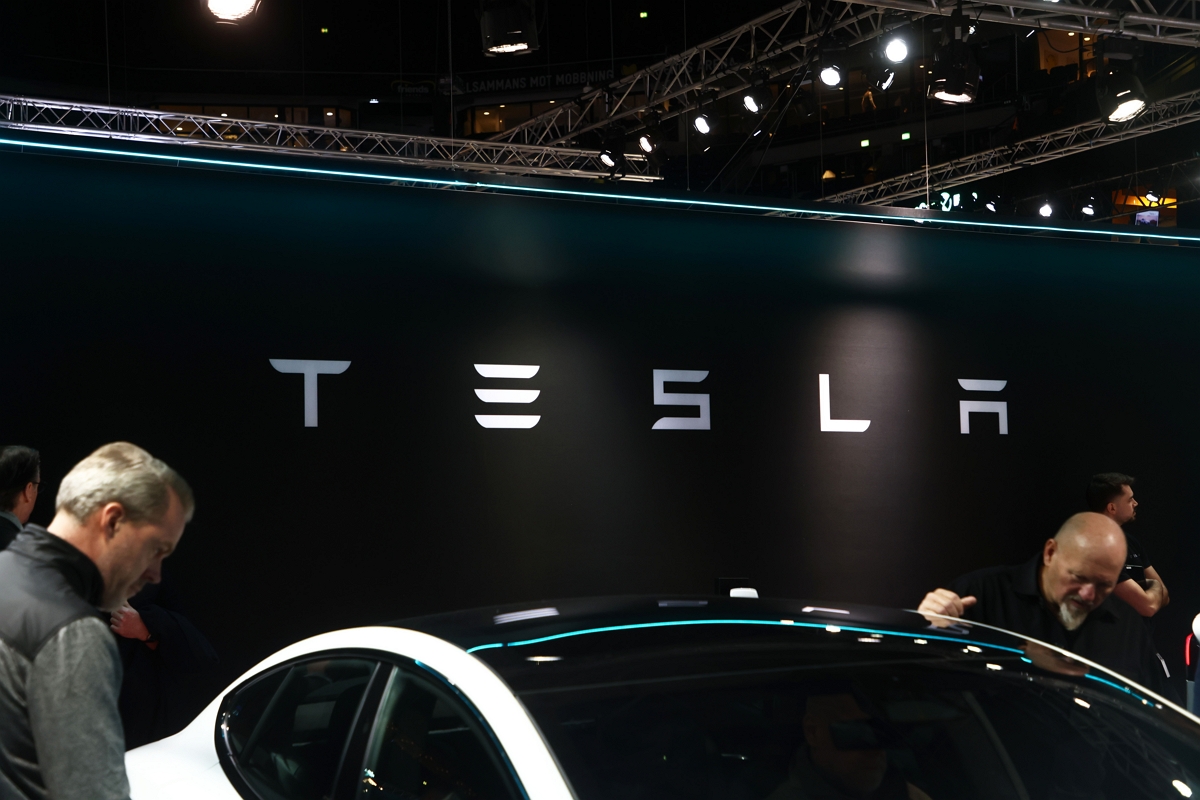
Tesla has announced plans to implement a next-generation dry battery electrode process this year that could cut production costs by 30%. This news is drawing attention from the battery industry, particularly as it comes three years ahead of South Korea’s projected 2028 commercialization timeline.
However, experts caution that the high technical complexity of this process makes successful commercialization uncertain. Some analysts predict that even if Tesla succeeds, the efficiency might not meet expectations.
According to industry sources on Wednesday, Tesla’s head of battery cell manufacturing recently boasted on social media about the company becoming the lowest-cost producer of battery cells per kilowatt-hour (kWh) by the end of last year.
Considering that he mentioned that Tesla will start manufacturing dry electrodes this year, it seems that Tesla is about to apply this process to its 4680 cylindrical batteries (46mm diameter, 80mm height).
This innovative process represents a leap forward in battery technology, employing high-temperature and high-pressure techniques to produce electrodes without organic solvents.
According to an October report from SNE Research, unlike conventional wet processes, the dry process is unnecessary, which can reduce costs by 30%, and the area required for the drying process can also be reduced by 50%.
The wet process takes up a lot of facility space and also costs a lot of electricity because the equipment used in the dry process is very long and generates hot air with electricity.
The report suggests that, in theory, it is possible to reduce the cost of 4680 cylindrical batteries using the dry process at a lower cost than lithium iron phosphate (LFP) batteries.
To date, no battery manufacturer has successfully mass-produced dry battery electrodes using this challenging technology. Industry insiders speculate that Tesla, which began developing the dry process in 2020, has struggled with low yield rates, hampering large-scale production.
While the industry remains skeptical about the near-term commercialization of the dry process, all eyes are on Tesla given its track record of innovation.
The company has already demonstrated its technological prowess by mainstreaming cylindrical form factors, once considered niche. Last year, Tesla captured 2.2% of the global battery market share (excluding China), ranking eighth overall.
If Tesla succeeds in commercializing this technology, it could significantly boost its in-house battery production through cost reductions, potentially putting pressure on existing battery manufacturers.
South Korea’s three major battery companies are also in the race to develop dry process technology. LG Energy Solution has already set up a pilot line at its Ochang Energy Plant in the fourth quarter of last year and aims to produce dry process batteries around 2028.
Some industry watchers remain skeptical, suggesting that even if Tesla succeeds, its efficiency might lag behind specialized battery manufacturers. It’s worth noting that Tesla currently sources batteries from LG Energy Solution and Panasonic.
An industry insider commented that while automakers may be able to internalize some battery production, achieving the economies of scale that dedicated battery companies enjoy is challenging. There are significant differences in technology, supply chains, and yield rates that can’t be easily overcome.